Сталь для ножей — Sandvik 12C27
19 Декабря 2011

Sandvik 12C27 — пожалуй, наиболее сбалансированная ножевая сталь, обладая одновременно отменными характеристиками заточки, высокой прочностью и устойчивостью к коррозии.
По словам компании производителя, Это наша основная марка стали для ручных ножей, коньковых лезвий high-end класса и ледовых буров. Вот уже на протяжении более чем 45 лет идёт работа над улучшением качества и технических показателей марки 12C27 . Структура становилась плотнее, степень чистоты — выше, а тонкая микроструктура карбида сегодня далека от той, что была в стали 12C27 в шестидесятых.
Рекомендованные области применения стали: охотничьи ножи, туристические ножи, карманные ножи, high-end кухонные ножи и тактические ножи.
Плотность стали составляет 7,7 гр / см3 .
Стандарты (в скобках указаны ближайшие соответствия):
ASTM (420)/(440A)
WNR (1.4034)/(1.4037)
Углерод (C) — 0,60%
Хром (Cr) — 13,5%
Молибден (Mo) —
Кремний (Si) = 0,40%
Марганец (Mn) — 0,40%
*Измерения происходят в условных единицах, обозначаемых HRC (или RC). Шкала прибора имеет разметку от 20 до 67 единиц. Твёрдость 60 единиц — самое высокое значение для ножа. Все, что свыше, означает, что нож твердый, но хрупкий. Поэтому большинство качественных клинков имеют твердость от 52 до 58 HRC.
Также рекомендуем ознакомиться с ножами EKA из стали 12С27
Широкий ассортимент разделочных и охотничьих ножей от шведской компании EKA. Качество — проверенное не только профессионалами, но и временем. С 1882 года ножи и инструменты, произведенные EKA, проходят жёсткий контроль качества и поставляются на рынок с 10-летней гарантией! Для изготовления лезвий используется шведская сталь Sandvick марки 12C27. Обращаем Ваше внимание на подробное описание и фото/видео материалы к каждой модели!
Нержавеющая сталь Sandvik 12C27 описание и характеристики



Области применения стали Sandvik 12C27:
- охотничьи ножи;
- туристические ножи;
- карманные ножи;
- high-end кухонные ножи;
- тактические ножи.
Измерения твердости стали ножей происходят в условных единицах, обозначаемых HRC (или RC). Шкала прибора имеет разметку от 20 до 67 единиц. Твёрдость 60 единиц — высшее значение для ножа по методу Роквелла. Все, что свыше, означает, что нож твердый, но хрупкий. Поэтому большинство качественных клинков имеют твердость от 52 до 58 HRC.
Sandvik 12C27 самая рекомендуемая сталь c диапазоном твердости 54-61 HRC, для производства высококачественных ножей для поваров и военных (тактических). Улучшенная ударная вязкость, отличное сохранение режущей кромки, хорошей антикоррозийностью и отличные характеристики заточки, сохраняющиеся в течение длительного времени. На основании многочисленных отзывов, стоит учитывать тот факт, что при производстве этой стали в Китае, ее технические характеристики могут сильно отличаться от Шведского, Финского и даже Бразильского производства.

Режущая кромка клинка из стали 12C27 (слева) и 440C (справа) — увеличение х1400. На 440C четко видны мощные карбиды, выполняющие роль «микропилы» (фото www.materials.sandvik).
Стандарты (в скобках указаны ближайшие соответствия):
- ASTM (420)/(440A)
- WNR (1.4034)/(1.4037)
Химический состав стали Sandvik 12C27 в % (номинальный):
- Углерод (C) — 0,60%
- Хром (Cr) — 13,5%
- Молибден (Mo) —
- Кремний (Si) = 0,40%
- Марганец (Mn) — 0,40%
Аналоги стали Sandvik 12C27
Российская сталь 65Х13 — признана одной из наиболее удобных, прочных и практичных в использовании сталей, с прекрасными антикоррозийными свойствами. Также по составу Sandvik 12C27 несколько похожа на германскую 1.4110, хотя в перечне аналогов зарубежные источники редко когда об этом упоминают. Ножи из стали Sandvik 12C27 — Смотреть
Ред. от 23.04.2020
Сталь Sandvik 12C27 шведская нержавеющая. Характеристики
Sandvik 12C27 ™ — шведская мартенситная нержавеющая хромистая сталь с оптимальным составом для высококачественных ножей.
Химический состав стали, %
C | Cr | Mo | Si | Mn |
0,60 | 13,5 | — | 0,4 | 0,4 |
После термообработки наличие в составе углерода и хрома дает уникальное сочетание свойств, в том числе:
- Очень высокая твердость
- Высокая прочность, вязкость
- Хорошая устойчивость к коррозии
- Очень высокая износостойкость
- Диапазон твердости 54-61 HRC
Sandvik 12C27 ™ используется для производства охотничьих и рыбацких ножей, складных ножей, ледобуров.
Ближайшие аналоги
- ASTM: (420), (440А)
- UNS: S42000
- W.Nr .: (1.4034), (1.4037)
Непрерывные улучшения в течение 45 лет переместили сталь в более высокий класс. Состав стал более точным, чистота намного выросла, а карбидная микроструктура сегодня далека от того, как выглядела сталь Sandvik 12C27 ™ в шестидесятых годах.
По потребительским свойствам сталь приближается к AUS 8 и ATS-34.Осуществляется доставка по всем регионам Российской Федерации: Московская область, Самара, Челябинская область, Свердловская область (Екатеринбург), Уфа (Республика Башкортостан), Республика Татарстан, Курганская область, Тюменская область, Пермский край, Оренбургская область, Краснодарский край, Удмуртская Республика и далее — все регионы России.
Наши менеджеры будут рады предоставить вам всю необходимую информацию.
Вся информация на сайте носит справочный характер и не является публичной офертой, определяемой положениями Статьи 437 Гражданского кодекса Российской Федерации. Технические параметры (спецификация) и комплект поставки товара могут быть изменены производителем.
Магазин Златоустовских украшенных изделий. Ножи Златоуста, Украшенное оружие, украшенная посуда. Часы, часы водолазные, секундомеры. © 2020 mybestbuy.ru
Виды и особенности ножевых марок стали
Поскольку сталь — это сплав железа и углерода, к которому могут быть добавлены некоторые другие примеси, разновидностей стали существует огромное множество. Естественно, в зависимости от точного состава, и качества разных марок этого металла существенно разнятся. Сегодня мы немного поговорим об особенностях наиболее популярных марок стали, которые используются в ножевом производстве. С учетом этих особенностей, вы сможете подобрать себе нож с такими характеристиками, которые наиболее полно будут соответствовать вашим запросам.
Не вся сталь используется для производства ножей. Ведь чтобы стать действительно подходящим материалом, она должна иметь определенные качества, которые были бы сбалансированы по отношению друг к другу. Одна из важных характеристик — это твердость металла. Она определяет способность стали противостоять деформации во время разрезания ножом других материалов. Измерить твердость можно разными способами. Соответственно, и единиц измерения существует несколько. Один из наиболее распространенных вариантов — использование шкалы Роквелла. Этот метод предполагает вдавливание в металл алмазной пирамидки под определенной нагрузкой и замер оставшегося оттиска. Основным элементом, влияющим на твердость, является углерод. Чем его больше, тем тверже получается металл. Однако, он также становится более восприимчивым к ржавчине, что для ножа уже не хорошо. Во многом, от твердости зависит износостойкость стали. Во время использования ножа, от него постоянно отделяются микрочастицы металла. Если износостойкость низкая, то режущая кромка быстро стирается, нож не только становится тупым, но и деформируется.
Прочность — еще одна важная характеристика металла. Речь идет о прочности металла на изгиб, необходимой, чтобы он остался невредимым после падения на пол, при неравномерном распределении нагрузок на отдельные части лезвия. В связи с этим, важно учитывать вязкость металла — его способность выдерживать импульсные нагрузки.
Три категории стали
Однако все эти характеристики не слишком понятны без конкретных примеров. Итак, марки сталей, которые используются для ножей, условно можно разделить на три категории. Основным фактором для их разделения служит процентное содержание углерода, от которого и зависят основные характеристики сплава.
Первая
В первую категорию входят стали с низким процентом углерода и не стабилизированные в достаточной мере легирующими добавками. На больших фабриках они используются для бюджетных моделей ножей. К данной категории относятся такие марки как 440А, 420 и 420НС, AUS-6, Sandvik 12C27. Главное преимущество всех сталей этой группы в том, что они имеют высокий уровень сопротивления коррозии. Ножи из таких сплавов хорошо подходят для использования в сырых условиях, могут использоваться для дайвинга, в том числе, и в соленой воде. Но все они слишком мягкие, чтобы нож мог долго оставаться острым. И в случае работы с твердыми материалами, их придется слишком часто затачивать. Сталь 440А содержит не более 0,75% углерода, 16-18% хрома, 1% марганца и 0,75% молибдена, закаливается до 55-57HRC. Если на ноже указано только число 440 без буквенного обозначения, речь также идет о стали 440А, как самой дешевой из своего семейства. Сплав 420HC содержит 0,46% углерода, 13% хрома, 0,3% ванадия, по 0,4% молибдена и кремния. Закалка этого металла производится в рамках 52-55HRC. Шведским аналогом этой марки является сталь Sandvik 12C27.
Это простая, но качественная сталь. Ее отличительная черта — высокая степень чистоты, которая достигается благодаря технологичной обработке сплава. Содержание в такой стали углерода составляет 0,6%, хрома — 13,5%, марганца и кремния — 0,4%. Из стали Sandvik производятся многие модели ножей Morakniv.
Вторая
Вторая группа — это стали с качеством Hi-end. В нее входят марки 440С, AUS-8, 8Cr13MoV, Sandvik 14C28N, VG-10. Они немного хуже справляются с противостоянием коррозии, поскольку уровень углерода в этих сплавах выше, но зато могут закаливаться до большей твердости и обладают более высокой износостойкостью. В сталь 440С добавлено 0,95-1,2% углерода, 16-18% хрома, 0,75% молибдена, по 1% марганца и кремния. Ее твердость составляет около 58-60HRC. Хотя следует учитывать, что испанская сталь этой же марки может быть несколько мягче. Сталь 440С используется для многих карманных ножей и при неплохих рабочих качествах является доступным по цене материалом. Широко использует такую марку стали компания Ganzo. Схожими с ней качествами обладает марка AUS-8. В такой стали содержится 0,7-0,75% углерода, 13-14,5% хрома, 0,49% никеля, 0,5% марганца, 1% кремния. Твердость закалки — 58HRC. Но нужно отметить, что хорошо работать с этой японской сталью умеют только японцы.
Марка 8Cr13MoV по сравнению с AUS-8 содержит больше углерода — 0,8%, и примерно такие же пропорции других легирующих добавок. Сталь закаливается до 58-59HRC. В целом, соотношение стоимости и качества у данной марки достаточно выгодное. А умелая обработка позволяет получить очень практичные ножи, например, как у бренда Spyderco.
Сталь Sandvik 14C28N имеет шведское происхождение. Разработку этого сплава заказала компания Kershaw, пожелавшая улучшить сплав 13C26. В итоге, в сталь включено 0,62% углерода, 14% хрома, 0,55% молибдена. Сталь имеет твердость 58-60HRC. Это один из лучших вариантов нержавейки для ножей стоимостью не более 30$.
VG-10 — сталь японского производства. Она широко применяется брендом Spyderco. Этот сплав отлично держит заточку, хотя режущую кромку нужно оберегать от импульсной нагрузки, иначе возможны сколы. В ней 0,95-1,05% углерода, 14,5-15,5% хрома, 1,4% кобальта, 1,05% молибдена, 0,5% марганца, 0,6% кремния. Твердость сплава очень высока — 59-61HRC.
Третья
Третья группа объединяет марки стали наилучшего качества. Среди самых известных марок этого уровня можно назвать Elmax и CPM S30VN. Elmax производится в Австрии. Она очень прочная, отлично держит заточку и относительно легко точится, ее твердость составляет 58-62HRC. Этот сплав содержит 1,7% углерода, 18% хрома, 1% молибдена, 0,8% хрома, 3% ванадия. Это порошковая сталь, которую многие знатоки считают лучшей для ножевой индустрии.
CPM S30VN получила 1,45% углерода, 14% хрома, 4% ванадия, 2% молибдена. Твердость ее закалки достигает 61HRC. Из такого сплава изготавливают высококачественные клинки верхнего ценового сегмента.
Влияние примесей
В характеристиках каждой из марок стали указано процентное содержание различных химических элементов, каждый из которых наделяет сплав теми или иными качествами. Как же разобраться в особенностях стали, зная ее состав?
Углерод
Углерод является основным элементом, помимо железа, для получения стали. Он способствует тому, что сталь можно закалить, влияет на твердость и прочность металла. Эти качества повышаются с увеличением количества углерода. Впрочем, одновременно возрастает и склонность к коррозии. Кухонные ножи и туристические бюджетного сегмента могут быть сделаны из стали с 0,4-0,6% углерода, но в более качественных — этот показатель выше.
Хром
Хром добавляют в сплав, чтобы повысить его стойкость к ржавчине. В нержавейках его не менее 14%. Но нужно сказать, что высокий процент примеси хрома снижает прочность металла.
Молибден
Молибден — одна из наиболее распространенных легирующих примесей. Он повышает жаропрочность сплава, усиливает стойкость к коррозии, которую дает хром. В целом, молибден позитивно влияет практически на все качества стали. Это обязательная составляющая для ножей, которые должны работать в агрессивной среде или при высоких температурах.
Кремний
Этот химический элемент снижает содержание кислорода в металле. Как следствие, повышается стойкость к ржавчине, прочность металла.
Кобальт
Кобальт добавляется в качестве примеси в твердые и быстрорежущие марки сталей. Необходимо отметить, что из кобальтосодержащих сталей изготавливают не только качественные ножи, но даже некоторые детали для космических ракет.
Ванадий
Ванадий существенно улучшает показатель износостойкости стали. Металл с этой примесью сложнее поддается заточке, но зато очень долго остается острым. А помимо того, он хорошо подходит для ножей, которые будут резать волокнистые материалы, ткани, войлок.
Марганец
Этот химический элемент существенно повышает твердость стали. Поэтому металл с его примесью используют не только для ножей, но и для производства сейфов, рельсов и прочих предметов, которые должны выдерживать большие нагрузки.
Вольфрам
Вольфрам обязательно входит в состав быстрорежущих сталей. Он существенно повышает жаропрочность сплава, а также его износостойкость и твердость.
Никель
Этот элемент улучшает стойкость металла к коррозии, а также повышает прочность стали. Его процентное содержание в стали не очень велико.
Теперь вы сможете свободнее ориентироваться в характеристиках ножей, которые известны исходя из того, какая марка стали используется для его производства. Эти знания помогут выбрать нож не только в соответствии с размерными параметрами и привлекательностью дизайна, но и с учетом его рабочих качеств, заложенных в стали.
14c28n vs. aus8 vs. 440C — Ножи
14c28n vs. aus8 vs. 440C — Ножи — Русскоязычный ножевой форум Jump to contentasi 516
-
- Users
- 516
- 7,060 posts
- Город: Ludwigsburg
- Имя: Александр
asi 516
-
- Users
- 516
- 7,060 posts
- Город: Ludwigsburg
- Имя: Александр
Russak 2,104
- ренегат
-
- Users
- 2,104
- 7,556 posts
- Город: Oldenburg
- Имя: Jewgeni
failbot 67
-
- Users
- 67
- 1,199 posts
- Город: Samara
- Имя: Sergey
asi 516
-
- Users
- 516
- 7,060 posts
- Город: Ludwigsburg
- Имя: Александр
asi 516
-
- Users
- 516
- 7,060 posts
- Город: Ludwigsburg
- Имя: Александр
Илья Анатольевич 351
-
- Users
- 351
- 2,165 posts
- Город: Екатеринбург
- Имя: CrossRaccoon
asi 516
-
- Users
- 516
- 7,060 posts
- Город: Ludwigsburg
- Имя: Александр
Илья Анатольевич 351
-
- Users
- 351
- 2,165 posts
- Город: Екатеринбург
- Имя: CrossRaccoon
failbot 67
-
- Users
- 67
- 1,199 posts
- Город: Samara
- Имя: Sergey
Ren Ren 4,229
-
- Users
- 4,229
- 16,044 posts
- Город: Москва
- Имя: Сергей
asi 516
-
- Users
- 516
- 7,060 posts
- Город: Ludwigsburg
- Имя: Александр
asi 516
-
- Users
- 516
- 7,060 posts
- Город: Ludwigsburg
- Имя: Александр
Типы сталей: Х12МФ и D2 — тверже твердого
Среди сталей используемых производителями ножей, одной из самых тяжелых в обработке и как следствие дающей самые надежные клинки является инструментальная сталь Х12МФ. Именно из этой стали изготавливают самые надежные охотничьи и туристические ножи.
Согласно ГОСТу сталь Х12МФ относится к штамповым инструментальным сталям. Применяется для создания вырубных и просечных штампов, дыропробивных матриц и матриц, имеющих сложную форму.
Главные характеристики этой стали: высокая механическая прочность, износоустойчивость, высокая режущая способность. Вырубные штампы для металла, изготовленные из этой стали не теряет своей остроты даже после вырубки нескольких тысяч заготовок.
Ножевые мастера, которые работают со сталью Х12МФ знают, что она тяжело поддается обработке и требует точного соблюдения процедуры закалки и отпуска.
Именно эти свойства стали Х12МФ по характеристикам приближают ее к булату. Здесь еще раз стоит оговориться и напомнить, что к легендарным особенностям булата относится высокая прочность и надежность, сопоставимая с чугунными сплавами. Но при этом сплав должен позволять изготавливать изделия методом ручной ковки. Ну и конечно, булатная сталь, обработанная в соответствии с правильной технологией, дает соответствующий булатный узор на клинке.
Довольно часто можно прочитать о том, что сталь Х12МФ называют литым булатом. Некоторые недобросовестные производители, изготавливающие ножи из этой стали (да и не только из этой) с помощью травления наносят на клинок узор, имитирующий булатный рисунок и предлагают покупателю такие ножи в качестве ножей из «булата».
Однако стоит обратить внимание на то, что такое сравнение возможно только в случае правильной термической обработки Х12МФ. У тех мастеров, кто профессионально занимается этим вопросом, есть свои секреты. Но те, кому удается выработать правильную технику закалки и отпуска приходят к тому, что на выходе получается клинок по твердости (63-62 HRC) сопоставимый с булатной сталью.
Режущая кромка такого ножа не выкрашивается и не создает заминов. Таким ножом можно разрубать гвозди и металлические уголки, протыкать толстостенные железные бочки. И при этом нож сохраняет целостность режущей кромки и свои рабочие характеристики.
Какая сталь лучше Х12МФ или D2?
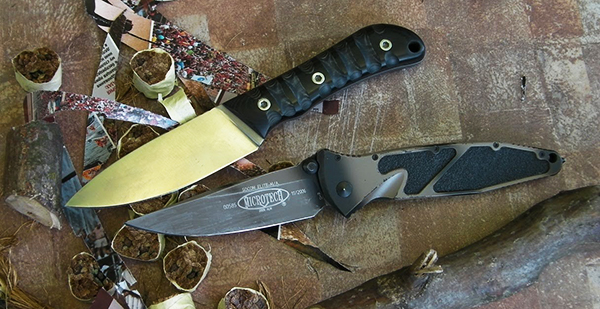
В интернете довольно часто возникают споры о том, можно ли сравнивать Х12МФ и американскую инструментальную сталь D2. О сравнении этих сталей не написал разве что ленивый, внесем и мы свою лепту. Кто-то хватил Х12МФ, а кто-то наоборот утверждает, что D2 дает более надежную режущую кромку. Правда, стоит учитывать, большинство таких споров основано на субъективных мнениях авторов, за которым обычно стоит привычное каждому человеку «нравится или не нравится».
Все становится на свои места, если взглянуть на химический состав этих сталей. Эти стали по своему составу являются аналогами. Российский классификатор сталей, также указывает, что зарубежным аналогом стали Х12МФ является сталь D2. Более того, сталь Х12МФ имеет большее в процентном соотношение содержание хрома. Именно этот такой состав, при определенной термической обработке дает высокий показатель твердости (63-62 HRC). Так что когда вы читаете о превосходстве D2 над Х12МФ — знайте, что автор скорее всего руководствуется субъективным и ни чем не подкрепленным мнением.
Приведенные данные позволяют нам говорить о том, что стали D2 и Х12МФ являются аналогами. А по некоторым характеристикам Х12МФ даже превосходит свой зарубежный аналог.
Ради интереса стоит обратить внимание на тот факт, что немногие западные компании изготавливают ножи из стали D2. Эта сталь, так же как и Х12МФ достаточно трудоемка в обработке. Например, компания COLD STEEL выпускает всего одну модель из этой стали Leatherneck. Это тактический нож, разработанный для подразделений морской пехоты США.
В России, где большинство ножей производятся на небольших кузнечных производствах, сталь Х12МФ более популярна и используется для создания надежных охотничьих ножей и ножей для выживания. Основные требования к такому ножу это высокая надежность (сломать нож можно, только если целенаправленно задаться такой целью) и долгое время сохранения остроты режущей кромки. Сталь Х12МФ отлично подходит для создания ножей такого типа.
— — Sandvik 1227 — Rezat.Ru
:- Английский
- ,
- ,
- ,
- Нож-

-
- ,
- ,
- , —
- (ЭДК)
- «»
- Mid-Tech
- —
- Benchmade
- Boker
- Бак ножи
- Холодная сталь
- CRKT
- Kershaw
- Microtech / Marfione
- Н.L. ножи
- Olamic столовые приборы
- Онтарио
- Pro-Tech
- Spyderco
- Нулевая терпимость
- ()
Свойства стального материала — SteelConstruction.info
Свойства конструкционной стали зависят как от ее химического состава, так и от способа производства, включая обработку во время изготовления. Стандарты на продукцию определяют пределы для состава, качества и производительности, и эти ограничения используются или предполагаются проектировщиками конструкций. В этой статье рассматриваются основные свойства, представляющие интерес для дизайнера, и указываются соответствующие стандарты для конкретных продуктов.Спецификация металлоконструкций рассматривается в отдельной статье.
Схематическая диаграмма напряжения / деформации для стали
[вверх] Свойства материала, необходимые для конструкции
Свойства, которые проектировщики должны учитывать при выборе изделий из стальных конструкций:
Для конструкции механические свойства получены из минимальных значений, указанных в соответствующем стандарте на продукцию.Свариваемость определяется химическим составом сплава, который регулируется стандартами на продукцию. Прочность зависит от типа сплава — обычная углеродистая сталь, атмосферостойкая сталь или нержавеющая сталь.
[вверх] Факторы, влияющие на механические свойства
Стальприобретает свои механические свойства благодаря сочетанию химического состава, термической обработки и производственных процессов. Хотя основной составляющей стали является железо, добавление очень небольших количеств других элементов может существенно повлиять на свойства стали.Прочность стали можно повысить, добавив такие сплавы, как марганец, ниобий и ванадий. Однако эти легирующие добавки могут также отрицательно повлиять на другие свойства, такие как пластичность, ударная вязкость и свариваемость.
Сведение к минимуму содержания серы может повысить пластичность, а ударную вязкость можно улучшить добавлением никеля. Поэтому химический состав для каждой спецификации стали тщательно сбалансирован и протестирован во время ее производства, чтобы гарантировать достижение соответствующих свойств.
Легирующие элементы также по-разному реагируют, когда материал подвергается термообработке, включающей охлаждение с заданной скоростью от определенной пиковой температуры. Производственный процесс может включать комбинации термообработки и механической обработки, которые имеют решающее значение для характеристик стали.
Механическая обработка осуществляется во время прокатки или формовки стали. Чем больше прокатывается стали, тем прочнее она становится. Этот эффект очевиден в стандартах на материалы, которые, как правило, указывают на снижение предела текучести с увеличением толщины материала.
Эффект термической обработки лучше всего объясняется с помощью различных технологических процессов, которые могут быть использованы при производстве стали, основными из которых являются:
- Сталь после проката
- Сталь нормализованная
- Сталь нормализованный прокат
- Сталь термомеханически прокатанная (ТМР)
- Закаленная и отпущенная (Q&T) сталь.
Сталь охлаждается во время прокатки, при этом типичная температура окончательной прокатки составляет около 750 ° C.Сталь, которой затем дают остыть естественным путем, называется материалом «после прокатки». Нормализация происходит, когда прокатанный материал снова нагревают примерно до 900 ° C и выдерживают при этой температуре в течение определенного времени, прежде чем дать ему возможность естественным образом остыть. Этот процесс позволяет уменьшить размер зерна и улучшить механические свойства, в частности, ударную вязкость. Нормализованная прокатка — это процесс, при котором после завершения прокатки температура превышает 900 ° C. Это имеет такое же влияние на свойства, как и нормализация, но исключает дополнительный процесс повторного нагрева материала.Нормализованные и нормализованные прокатные стали имеют обозначение «N».
Использование высокопрочной стали может уменьшить объем необходимой стали, но сталь должна быть прочной при рабочих температурах, а также должна обладать достаточной пластичностью, чтобы противостоять любому распространению вязких трещин. Следовательно, стали с более высокой прочностью требуют улучшенной ударной вязкости и пластичности, которые могут быть достигнуты только с использованием низкоуглеродистых чистых сталей и за счет максимального измельчения зерна. Реализация процесса термомеханической прокатки (TMR) является эффективным способом достижения этой цели.
Термомеханический прокат в стали использует особый химический состав стали, что обеспечивает более низкую конечную температуру прокатки около 700 ° C. Для прокатки стали при этих более низких температурах требуется большее усилие, и свойства сохраняются, если повторно не нагреть сталь выше 650 ° C. Сталь, подвергнутая термомеханическому прокату, имеет обозначение «М».
Процесс обработки закаленной и отпущенной стали начинается с нормализованного материала при температуре 900 ° C. Он быстро охлаждается или закаливается для производства стали с высокой прочностью и твердостью, но с низкой вязкостью.Прочность восстанавливается повторным нагревом до 600 ° C, поддержанием температуры в течение определенного времени и затем естественным охлаждением (отпуск). Закаленная и отпущенная сталь обозначается буквой Q.
Закалка включает быстрое охлаждение продукта путем погружения непосредственно в воду или масло. Он часто используется в сочетании с отпуском, который представляет собой термообработку на второй стадии до температур ниже диапазона аустенизации. Эффект отпуска заключается в смягчении ранее затвердевших структур и их повышении прочности и пластичности.
Схематический график температуры / времени процессов прокатки
[наверх] Прочность
[вверху] Предел текучести
Предел текучести — это наиболее распространенное свойство, которое может понадобиться проектировщику, поскольку это основа, используемая для большинства правил, приведенных в нормах проектирования. В европейских стандартах для конструкционных углеродистых сталей (включая погодостойкую сталь) основное обозначение относится к пределу текучести, т.е.грамм. Сталь S355 — это конструкционная сталь с указанным минимальным пределом текучести 355 Н / мм².
Стандарты на продукцию также определяют допустимый диапазон значений предела прочности на разрыв (UTS). Минимальный UTS имеет отношение к некоторым аспектам дизайна.
[вверх] Горячекатаный прокат
Для горячекатаных углеродистых сталей цифра в обозначении представляет собой значение предела текучести для материала толщиной до 16 мм. Конструкторам следует учитывать, что предел текучести уменьшается с увеличением толщины листа или секции (более тонкий материал обрабатывается больше, чем толстый материал, и обработка увеличивает прочность).Для двух наиболее распространенных марок стали, используемых в Великобритании, указанные минимальный предел текучести и минимальный предел прочности на растяжение показаны в таблице ниже для сталей в соответствии с BS EN 10025-2 [1] .
Марка | Предел текучести (Н / мм 2 ) для номинальной толщины t (мм) | Предел прочности на разрыв (Н / мм 2 ) для номинальной толщины t (мм) | ||||
---|---|---|---|---|---|---|
т ≤ 16 | 16 | 40 | 63 | 3 | 100 | |
S275 | 275 | 265 | 255 | 245 | 410 | 400 |
S355 | 355 | 345 | 335 | 325 | 470 | 450 |
Национальное приложение Великобритании к BS EN 1993-1-1 [2] позволяет использовать минимальное значение текучести для конкретной толщины в качестве номинального (характеристического) предела текучести f y и минимального значения прочности на растяжение прочность f u использовать как номинальный (характеристический) предел прочности.
Подобные значения приведены для других марок в других частях BS EN 10025 и для полых профилей в соответствии с BS EN 10210-1 [3] .
[вверх] Холодногнутые стали
Существует широкий диапазон марок стали для полосовой стали, пригодной для холодной штамповки. Минимальные значения предела текучести и предела прочности указаны в соответствующем стандарте на продукцию BS EN 10346 [4] .
BS EN 1993-1-3 [5] содержит значения базового предела текучести f yb и предела прочности на растяжение f u , которые должны использоваться в качестве характерных значений при проектировании.
[вверх] Нержавеющая сталь
Марки нержавеющей стали обозначаются числовым «номером стали» (например, 1.4401 для типичной аустенитной стали), а не системой обозначений «S» для углеродистых сталей. Зависимость «напряжение-деформация» не имеет четкого различия между пределом текучести, и «предел текучести» нержавеющей стали для нержавеющей стали обычно указывается в терминах предела текучести, определенного для конкретной остаточной деформации смещения (обычно 0,2% деформации).
Прочность обычно используемых конструкционных нержавеющих сталей составляет от 170 до 450 Н / мм². Аустенитные стали имеют более низкий предел текучести, чем обычно используемые углеродистые стали; Дуплексные стали имеют более высокий предел текучести, чем обычные углеродистые стали. Как для аустенитных, так и для дуплексных нержавеющих сталей отношение предела прочности к пределу текучести больше, чем для углеродистых сталей.
BS EN 1993-1-4 [6] содержит в таблице номинальные (характеристические) значения предела текучести f y и минимального предела прочности на растяжение f u для сталей согласно BS EN 10088-1 [7] для использование в дизайне.
[вверх] Прочность
Образец для испытаний на удар с V-образным надрезом
Все материалы имеют дефекты. В стали эти дефекты принимают форму очень маленьких трещин. Если сталь недостаточно прочная, «трещина» может быстро распространяться без пластической деформации и привести к «хрупкому разрушению». Риск хрупкого разрушения увеличивается с увеличением толщины, растягивающего напряжения, концентраторов напряжений и при более низких температурах.Вязкость стали и ее способность противостоять хрупкому разрушению зависят от ряда факторов, которые следует учитывать на этапе спецификации. Удобной мерой прочности является испытание на удар по Шарпи с V-образным надрезом — см. Изображение справа. В ходе этого испытания измеряется энергия удара, необходимая для разрушения небольшого образца с надрезом при заданной температуре одним ударом маятника.
В различных стандартах на продукцию указываются минимальные значения энергии удара для различных классов прочности каждого класса прочности.Для нелегированных конструкционных сталей основными обозначениями марок стали JR, J0, J2 и K2. Для мелкозернистых сталей, закаленных и отпущенных сталей (которые обычно более жесткие, с более высокой энергией удара) используются разные обозначения. Краткое описание обозначений ударной вязкости приведено в таблице ниже.
Стандартный | Подкладка | Ударная вязкость | Температура испытания |
---|---|---|---|
BS EN 10025-2 [1] BS EN 10210-1 [3] | JR | 27J | 20 o С |
J0 | 27J | 0 o С | |
J2 | 27J | -20 o С | |
K2 | 40J | -20 o С | |
BS EN 10025-3 [8] | N | 40J | -20 o с |
NL | 27J | -50 o с | |
BS EN 10025-4 [9] | M | 40J | -20 o с |
ML | 27J | -50 o с | |
BS EN 10025-5 [10] | J0 | 27J | 0 o С |
J2 | 27J | -20 o С | |
K2 | 40J | -20 o С | |
J4 | 27J | -40 o С | |
J5 | 27J | -50 o С | |
BS EN 10025-6 [11] | Q | 30J | -20 o с |
QL | 30J | -40 o с | |
QL1 | 30J | -60 o c |
Для тонкостенных сталей для холодной штамповки не предъявляются требования к энергии удара для материала толщиной менее 6 мм.
Выбор подходящего подкласса для обеспечения соответствующей прочности в расчетных ситуациях приведен в BS EN 1993‑1‑10 [12] и связанном с ним UK NA [13] . Правила связывают температуру воздействия, уровень напряжения и т. Д. С «предельной толщиной» для каждого подкласса стали. PD 6695-1-10 [14] содержит полезные справочные таблицы, а руководство по выбору подходящего подкласса дано в ED007.
Эти правила проектирования были разработаны для конструкций, подверженных усталости, таких как мосты и несущие конструкции кранов, и признано, что их использование в зданиях, где усталость играет второстепенную роль, является чрезвычайно безопасным.
Публикация SCI P419 представляет модифицированные пределы толщины стали, которые могут использоваться в зданиях, где усталость не учитывается при проектировании. Эти новые пределы были получены с использованием того же подхода, что и правила проектирования Еврокода, но существенно снижают рост трещин из-за усталости. Используется слово «уменьшить», поскольку предполагать, что никакого роста вообще нет, значило бы полностью устранить эффект утомления. Допускается некоторая усталость (20 000 циклов) на основании ориентировочных указаний стандарта DIN.
Термин «квазистатический» будет охватывать такие конструкции — в действительности, может иметь место некоторая ограниченная цикличность нагрузки, но это обычно не рассматривается — подход к проектированию состоит в том, чтобы рассматривать все нагрузки как статические. Ключом к новому подходу является формула для выражения роста трещины за период до 20 000 циклов. Эксперты из Ахенского университета (участвовавшие в разработке Еврокода) дали это важнейшее выражение.
Дополнительная информация доступна в технической статье в сентябрьском номере журнала NSC за 2017 год.
Нержавеющая сталь обычно намного прочнее углеродистой стали; минимальные значения указаны в BS EN 10088-4 [15] . BS EN 1993-1-4 [6] утверждает, что аустенитные и дуплексные стали достаточно прочны и не подвержены хрупкому разрушению при рабочих температурах до -40 ° C.
[вверху] Пластичность
Пластичность — это мера степени, в которой материал может деформироваться или растягиваться между началом текучести и возможным разрушением под действием растягивающей нагрузки, как показано на рисунке ниже.Конструктор полагается на пластичность для ряда аспектов проектирования, включая перераспределение напряжений в предельном состоянии, конструкцию группы болтов, снижение риска распространения усталостной трещины и в производственных процессах сварки, изгиба и правки. Различные стандарты для марок стали в приведенной выше таблице настаивают на минимальном значении пластичности, поэтому проектные предположения являются действительными, и если они указаны правильно, проектировщик может быть уверен в их адекватных характеристиках.
Напряжение — деформация стали
[вверх] Свариваемость
Приваривание ребер жесткости к большой сборной балке
(Изображение любезно предоставлено Mabey Bridge Ltd)
Все конструкционные стали в основном поддаются сварке. Однако сварка предполагает локальное плавление стали, которая впоследствии остывает.Охлаждение может быть довольно быстрым, поскольку окружающий материал, например балка обеспечивает большой «теплоотвод», а сварной шов (и вводимое тепло) обычно относительно невелик. Это может привести к упрочнению «зоны термического влияния» (HAZ) и снижению ударной вязкости. Чем больше толщина материала, тем больше снижение ударной вязкости.
Склонность к охрупчиванию также зависит от легирующих элементов, главным образом, но не исключительно, от содержания углерода. Эту восприимчивость можно выразить как «эквивалентное значение углерода» (CEV), и различные стандарты продукции для углеродистой стали содержат выражения для определения этого значения.
BS EN 10025 [1] устанавливает обязательные пределы для CEV для всех покрываемых конструкционных стальных изделий, и это простая задача для тех, кто контролирует сварку, чтобы гарантировать, что используемые спецификации процедуры сварки соответствуют соответствующей марке стали и CEV.
[вверх] Прочие механические свойства стали
Другие важные для проектировщика механические свойства конструкционной стали включают:
- Модуль упругости, E = 210 000 Н / мм²
- Модуль сдвига, G = E / [2 (1 + ν )] Н / мм², часто принимается равным 81 000 Н / мм²
- Коэффициент Пуассона, ν = 0.3
- Коэффициент теплового расширения, α = 12 x 10 -6 / ° C (в диапазоне температур окружающей среды).
[вверху] Прочность
Нанесение защиты от коррозии на месте
(Изображение любезно предоставлено Hempel UK Ltd.)
Еще одним важным свойством является защита от коррозии. Хотя доступны специальные коррозионно-стойкие стали, они обычно не используются в строительстве.Исключением является погодостойкая сталь.
Наиболее распространенными способами защиты конструкционной стали от коррозии являются окраска или гальваника. Требуемый тип и степень защиты покрытия зависит от степени воздействия, местоположения, расчетного срока службы и т. Д. Во многих случаях во внутренних сухих условиях не требуется никаких антикоррозионных покрытий, кроме соответствующей противопожарной защиты. Доступна подробная информация о защите от коррозии конструкционной стали.
[вверх] Погодостойкая сталь
Погодоустойчивая сталь — это высокопрочная низколегированная сталь, которая противостоит коррозии, образуя прилипшую защитную ржавчину «патину», которая препятствует дальнейшей коррозии.Защитное покрытие не требуется. Он широко используется в Великобритании для строительства мостов и некоторых зданий. Он также используется для архитектурных элементов и скульптурных сооружений, таких как Ангел Севера.
Ангел Севера
[вверху] Нержавеющая сталь
Типичные кривые напряжение-деформация для нержавеющей и углеродистой стали в отожженном состоянии
Нержавеющая сталь — это материал с высокой коррозионной стойкостью, который можно использовать в конструкциях, особенно там, где требуется высококачественная обработка поверхности.Подходящие степени воздействия в типичных условиях окружающей среды приведены ниже.
Поведение нержавеющих сталей при напряжении и деформации отличается от углеродистых сталей во многих отношениях. Наиболее важное различие заключается в форме кривой напряжения-деформации. В то время как углеродистая сталь обычно демонстрирует линейное упругое поведение вплоть до предела текучести и плато перед деформационным упрочнением, нержавеющая сталь имеет более округлую реакцию без четко определенного напряжения текучести. Следовательно, предел текучести нержавеющей стали обычно определяется для конкретной остаточной деформации смещения (обычно 0.2% деформации), как показано на рисунке справа, на котором показаны типичные экспериментальные кривые напряжение-деформация для обычных аустенитных и дуплексных нержавеющих сталей. Показанные кривые представляют диапазон материалов, которые могут быть поставлены, и не должны использоваться при проектировании.
Описание | Марка | Минимум 0.Предел текучести 2% (Н / мм 2 ) | Предел прочности на разрыв (Н / мм 2 ) | Относительное удлинение при разрыве (%) |
---|---|---|---|---|
Основные хромоникелевые аустенитные стали | 1.4301 | 210 | 520–720 | 45 |
1.4307 | 200 | 500–700 | 45 | |
Молибден-хромникелевые аустенитные стали | 1.4401 | 220 | 520–670 | 45 |
1.4404 | 220 | 520–670 | 45 | |
Дуплексные стали | 1,4162 | 450 | 650–850 | 30 |
1.4462 | 460 | 640–840 | 25 |
Механические свойства относятся к горячекатаному листу. Для холоднокатаной и горячекатаной полосы указанные значения прочности на 10-17% выше.
BS EN ISO 9223 [16] Класс атмосферной коррозии | Типичная внешняя среда | Подходящая нержавеющая сталь |
---|---|---|
C1 (Очень низкий) | Пустыни и арктические районы (очень низкая влажность) | 1.4301 / 1.4307, 1.4162 |
C2 (Низкий) | Засушливые или низкие уровни загрязнения (сельские районы) | 1.4301 / 1.4307, 1.4162 |
C3 (средний) | Прибрежные районы с небольшими отложениями соли Городские или промышленные районы с умеренным загрязнением | 1.4401 / 1.4404, 1.4162 (1.4301 / 1.4307) |
C4 (высокий) | Загрязненная городская и промышленная атмосфера Прибрежные районы с умеренными солевыми отложениями Дорожная среда с солями для защиты от обледенения | 1.4462, (1.4401 / 1.4404), другие более высоколегированные дуплексы или аустенитные материалы |
C5 (Очень высокий) | Сильно загрязненная промышленная среда с высокой влажностью Морская среда с высокой степенью солевых отложений и брызг | 1.4462, другие более высоколегированные дуплексы или аустенитные материалы |
Материалы, подходящие для более высокого класса, могут использоваться для более низких классов, но могут быть неэффективными с точки зрения затрат. Материалы в скобках можно рассмотреть, если допустима умеренная коррозия. Накопление коррозионных загрязнителей и хлоридов будет выше в защищенных местах; следовательно, может потребоваться выбрать рекомендуемый сорт из следующего более высокого класса коррозии.
[вверху] Каталожные номера
- ↑ 1.0 1,1 1,2 BS EN 10025-2: 2019 Горячекатаный прокат из конструкционных сталей. Технические условия поставки нелегированных конструкционных сталей, BSI.
- ↑ NA + A1: 2014 к BS EN 1993-1-1: 2005 + A1: 2014, Национальное приложение Великобритании к Еврокоду 3: Проектирование стальных конструкций Общие правила и правила для зданий, BSI
- ↑ 3,0 3,1 BS EN 10210-1: 2006 Горячекатаные полые профили конструкционные из нелегированных и мелкозернистых сталей. Технические требования к поставке, BSI.
- ↑ BS EN 10346: 2015 Плоский стальной прокат с непрерывным горячим покрытием для холодной штамповки. Технические условия поставки. BSI
- ↑ BS EN 1993-1-3: 2006 Еврокод 3: Проектирование стальных конструкций. Общие правила — Дополнительные правила для холодногнутых профилей и листов, BSI.
- ↑ 6,0 6,1 BS EN 1993-1-4: 2006 + A1: 2015 Еврокод 3. Проектирование стальных конструкций. Основные правила. Дополнительные правила для нержавеющих сталей, BSI
- ↑ BS EN 10088-1: 2014 Нержавеющие стали.Список нержавеющих сталей, BSI
- ↑ BS EN 10025-3: 2019, Горячекатаный прокат из конструкционных сталей, Часть 3: Технические условия поставки нормализованных / нормализованных прокатных свариваемых мелкозернистых конструкционных сталей, BSI
- ↑ BS EN 10025-4: 2019, Горячекатаный прокат из конструкционных сталей, Часть 4: Технические условия поставки для термомеханического проката свариваемых мелкозернистых конструкционных сталей, BSI
- ↑ BS EN 10025-5: 2019, Горячекатаный прокат из конструкционных сталей, Часть 5: Технические условия поставки для конструкционных сталей с повышенной стойкостью к атмосферной коррозии, BSI
- ↑ BS EN 10025-6: 2019, Горячекатаный прокат из конструкционных сталей, Часть 6: Технические условия поставки плоского проката из конструкционных сталей с высоким пределом текучести в закаленном и отпущенном состоянии, BSI
- ↑ BS EN 1993-1-10: 2005 Еврокод 3.Проектирование металлоконструкций. Вязкость материала и свойства по толщине, BSI.
- ↑ NA к BS EN 1993-1-10: 2005, Национальное приложение Великобритании к Еврокоду 3: Проектирование стальных конструкций. Прочность материала и свойства по толщине. BSI
- ↑ PD 6695-1-10: 2009 Рекомендации по проектированию конструкций согласно BS EN 1993-1-10. BSI
- ↑ 15,0 15,1 BS EN 10088-4: 2009 Нержавеющие стали. Технические условия поставки листов и полос из коррозионно-стойких сталей строительного назначения, BSI.
- ↑ BS EN ISO 9223: 2012 Коррозия металлов и сплавов, Коррозионная активность атмосферы, Классификация, определение и оценка. BSI
[вверх] Ресурсы
[вверху] См. Также
,Введение в усовершенствованные высокопрочные стали
В части I этой серии из двух частей представлен обзор марок усовершенствованных высокопрочных сталей (AHSS). Part II решает проблемы, возникающие при обработке этих сортов.Несколько новых серийно выпускаемых и почти серийно выпускаемых усовершенствованных высокопрочных сталей (AHSS), которые демонстрируют высокую прочность и улучшенную формуемость, предлагаются по всему миру. Эти стали могут снизить стоимость и вес при одновременном повышении производительности.
Повышенная формуемость позволяет усложнять детали, что приводит к меньшему количеству отдельных деталей (экономия затрат) и большей гибкости производства. Меньшее количество деталей означает меньше сварочных работ (экономия затрат и времени цикла) и сварных фланцев (снижение массы и веса). В зависимости от конструкции более высокая прочность может приводить к повышению утомляемости и ударопрочности при сохранении или даже снижении толщина.
Марка стали | YS (МПа) | ОТС (МПа) | Всего EL (%) | n Значение (5-15%) | r Штанга | К Значение (МПа) |
BH 210/340 | 210 | 340 | 34-39 | 0.18 | 1,8 | 582 |
BH 260/370 | 260 | 370 | 29-34 | 0,13 | 1,6 | 550 |
DP 280/600 | 280 | 600 | 30-34 | 0,21 | 1 | 1,082 |
IF 300/420 | 300 | 420 | 29-36 | 0.2 | 1,6 | 759 |
DP 300/500 | 300 | 500 | 30-34 | 0,16 | 1 | 762 |
HSLA 350/450 | 350 | 450 | 23–27 | 0,14 | 1,1 | 807 |
DP 350/600 | 350 | 600 | 24-30 | 0.14 | 1 | 976 |
DP 400/700 | 400 | 700 | 19-25 | 0,14 | 1 | 1,028 |
Поездка 450/800 | 450 | 800 | 26-32 | 0,24 | 0,9 | 1,690 |
DP 500/800 | 500 | 800 | 14-20 | 0.14 | 1 | 1 303 |
CP 700/800 | 700 | 800 | 10-15 | 0,13 | 1 | 1,380 |
DP 700/1000 | 700 | 1 000 | 12-17 | 0,09 | 0,9 | 1,521 |
Март 950/1200 | 950 | 1,200 | 5-7 | 0.07 | 0,9 | 1,678 |
Март 1250/1520 | 1,250 | 1,520 | 4-6 | 0,065 | 0,9 | 2,021 |
Рисунок 1
Свойства стали
YS и UTS являются минимальными значениями, другие значения являются типичными.
Источник: ULSAB-AVC TTD № 6 (Сообщение о передаче технологии № 6)
доступно на сайте www.ULSAB-AVC.org или www.autosteel.org.
В первой части этой серии из двух частей исследуются сходства и различия между обычной HSS и различными сортами AHSS. На рис. 1 перечислены некоторые механические свойства марок, обсуждаемых в этой статье. Значения, приведенные в таблице, приведены только для сравнения, при этом конкретные свойства и диапазоны, вероятно, несколько различаются в зависимости от металлургических компаний. Кроме того, значение n — это Функция рассчитывается в определенном диапазоне деформации и более подвержена изменению в зависимости от выбранного диапазона деформации для марок AHSS по сравнению с обычными марками HSS.В результате важно учитывать данные из соответствующего диапазона деформации, относящиеся к конкретной операции формовки.
Обычные высокопрочные стали
Принято считать, что переход от низкоуглеродистой стали к быстрорежущей стали происходит при пределе текучести около 210 мегапаскалей (МПа) [30 фунтов на квадратный дюйм (KSI)]. Для уровней предела текучести ниже 280–350 МПа (от 40 до 50 KSI) обычно используется простая углеродисто-марганцевая (CMn) сталь. По составу эти стали аналогичны низкоуглеродистым мягким сталям, за исключением того, что в них больше углерода и марганец для увеличения прочности до нужного уровня.Этот подход обычно непрактичен для пределов текучести выше 350 МПа (50 KSI) из-за снижения удлинения и свариваемости.
Один из подходов к достижению предела текучести от 280 до 550 МПа (от 40 до 80 KSI) заключается в использовании высокопрочных низколегированных сталей (HSLA), также известных как микролегированные (MA) стали. Это семейство сталей обычно имеет микроструктуру из мелкозернистого феррита, упрочненного углеродными и / или азотными выделениями титана, ванадия или ниобия (колумбия).Добавление марганца, фосфора или кремний еще больше увеличивает прочность. Эти стали можно успешно формовать, если пользователи знают об ограничениях компромисса с более высокой прочностью и меньшей формуемостью.
Другой подход к достижению этих уровней предела текучести — использование марок AHSS. Двухфазная (DP), пластичность, вызванная трансформацией (TRIP), высокое расширение отверстий (HHE), комплексно-фазовая (CP) и мартенситная стали — это некоторые из марок, которые в совокупности называются AHSS.
Двухфазные (DP) Стали
Рисунок 2 Прочность сформированной панели Источник: J.Р. Шоу, К. Ватанабе и М. Чен, «Определение характеристик процесса обработки металлов давлением и моделирование современных высокопрочных сталей», Общество инженеров автомобильной промышленности (SAE), 2001-01-1139. |
Стали DP имеют микроструктуру, состоящую в основном из мягкого феррита с разбросанными по всей поверхности островками твердого мартенсита. Уровень прочности этих марок зависит от количества мартенсита в микроструктуре.
Когда продукт поступает со сталеплавильного завода, его предел текучести обычно намного ниже, чем его предел текучести, с отношением YS-to-TS около 0.6. (Для сравнения, отношение YS-to-TS для сталей HSLA ближе к 0,75.) Более низкий предел текучести при заданном пределе прочности приводит к более высоким значениям удлинения и лучшей формуемости.
Кроме того, реакция наклепа на деформацию различается для сталей DP и HSLA. Стали HSLA начинают терять формуемость, как только начинается деформация. Благодаря мягкой ферритовой матрице сталей DP они могут сохранять формуемость и дальше во время рабочего хода пресса и могут лучше распределять деформации по детали.
СталиDP обычно подвергаются прокаливанию (упрочнение происходит после того, как сталь проходит цикл покраски и выпечки), тогда как стали HSLA не обладают этой характеристикой (, рис. 2, ). Между такой прокаливаемой способностью и более высоким уровнем деформируемой прокаливаемости нет ничего необычного в увеличении предела текучести примерно на 140 МПа (20 KSI) после формования и прокаливания. Для сравнения, HSLA стали могут иметь повышение примерно на 20 МПа (3 KSI).
Повышенное поглощение энергии — еще одна характеристика стали DP.Для данного предела текучести прочность на разрыв стали DP выше, чем у сталей HSLA, что улучшает характеристики при столкновении. Если требуются характеристики ударопрочности, эквивалентные характеристикам стали HSLA, использование стали DP может обеспечить снижение прочности примерно на 10 процентов. 1
Свариваемость сталиDP обычно аналогична свариваемости сталей HSLA, хотя могут потребоваться другие параметры. Диапазон сварочного тока почти такой же (около 3 килоампер), но фактические токи могут несколько смещаться. 2
Рисунок 3 Кривые напряжение-деформация для сталей HSLA, DP и TRIP [Предел текучести 350 МПа (50 KSI)] Источник: A. Konieczny, «Улучшенные высокопрочные стали — формуемость», Семинар по большим конструкциям в стали, февраль 2003 г., Американский институт черной металлургии, и Рекомендации AHSS на сайте www.WorldAutoSteel. орг. |
Стали с трансформационной пластичностью (TRIP)
Как и стали DP, микроструктура сталей TRIP состоит в основном из мягкого феррита.В то время как стали DP содержат мартенсит как единственную другую фазу, стали TRIP содержат комбинацию мартенсита, бейнита и остаточного аустенита. Различные уровни этих фаз придают сталям TRIP уникальный баланс свойств. На рисунке 3 показаны кривые напряжение-деформация для стали HSLA, стали DP, и сталь TRIP, каждая с пределом текучести около 350 МПа (50 KSI).
По мере продолжения формовки остаточный аустенит в TRIP постепенно превращается в мартенсит с увеличением деформации.Это приводит к изменению объема и формы внутри микроструктуры, что компенсирует деформацию и увеличивает пластичность. В сталях TRIP высокая скорость деформационного упрочнения сохраняется при более высоких деформациях, в то время как в сталях DP начинает снижаться. Эта разница в деформационном упрочнении является одним из основные причины улучшенной формуемости сталей DP по сравнению со сталями HSLA, и что дает сталям TRIP дополнительное преимущество перед сталями DP (, рис. 4 ).
Уровень деформации превращения остаточного аустенита в мартенсит может быть спроектирован путем регулирования содержания углерода.Если используются более низкие уровни углерода, превращение начинается в начале формования, что приводит к отличной формуемости и распределению деформации на полученных уровнях прочности. При более высоком содержании углерода остаточный аустенит более стабилен и сохраняется в конечной части. трансформация происходит при уровнях деформации, превышающей те, которые возникают во время штамповки и формовки. Превращение в мартенсит происходит во время последующей деформации, такой как авария, и обеспечивает большее поглощение энергии аварии.
Рисунок 4 Деформационное упрочнение сталей HSLA, DP и TRIP Источник: А. Конечны, «Передовые высокопрочные стали — формуемость», Семинар по большим конструкциям в стали, февраль 2003 г., Американский институт черной металлургии; Рекомендации AHSS доступны на сайте www.WorldAutoSteel.org. |
Дополнительное легирование, необходимое для получения эффекта TRIP, делает точечную сварку более сложной задачей по сравнению со сталями DP.Эту проблему можно решить с помощью модифицированных сварочных циклов.
Стали с большим расширением отверстий (HHE), также известные как высокопрочные стали для эластичных отбортовок (SFHS)
Для применений, где требуется высокая степень удлинения кромок при срезе (отбортовка отверстий), все чаще используются стали HHE. Микроструктура в основном состоит из феррита и бейнита с некоторым количеством остаточного аустенита. Эти стали обладают высокой прочностью, высокой формуемостью (хотя и меньшей, чем у некоторых других марок AHSS) и возможностью большого удлинения кромки при сдвиге (отбортовка отверстий).Ферритно-бейнитный микроструктура связана с высокими значениями расширения отверстия. Штампованные детали из этих марок заменяют литые и кованые детали из других материалов.
Стали сложной фазы (CP)
СталиCP характеризуются очень тонкой микроструктурой феррита и более высокой объемной долей твердых фаз (мартенсита и бейнита), дополнительно упрочненных мелкими углеродными или азотными осадками ниобия, титана или ванадия.
Эти марки стали используются для изготовления деталей, требующих высокой способности поглощать энергию, таких как бамперы и усиление средней стойки.
Мартенситные стали
Мартенситная стальимеет микроструктуру, которая на 100% состоит из мартенсита. Минимальная прочность на растяжение этого семейства сталей обычно составляет от 900 до 1500 МПа (130 и 220 KSI). Эти марки могут быть получены непосредственно на сталеплавильном заводе (закалка после отжига) или путем термообработки после формования. Из-за своего ограниченного удлинения мартенсит, полученный на заводе, обычно формуют прокаткой. Более сложный формы могут быть изготовлены путем горячей штамповки и закалки с углеродом с более низким содержанием углерода.
В зависимости от заданного уровня прочности эти марки могут иметь содержание углерода, типичное для низкоуглеродистой стали, или более 0,20 процента. Марганец, кремний, хром, молибден, бор, ванадий и никель также используются в различных комбинациях для повышения прокаливаемости. В результате может потребоваться корректировка процедуры сварки.
Типичными областями применения мартенситных сталей обычно являются те, которые требуют высокой прочности и хорошего сопротивления усталости, с относительно простым поперечным сечением (хотя профили горячештампованных деталей становятся более сложными).Хорошими кандидатами на роль мартенситных деталей являются дверные балки, усиливающие балки бампера, усилители боковых порогов и усиления поясной линии.
Увеличение числа приложений
В сочетании с соответствующими технологиями производства передовые высокопрочные стали предлагают возможности для снижения веса продукта, повышения ударопрочности, консолидации производственного процесса и снижения затрат.
Эти конструкционные стали находят все большее применение в различных отраслях обрабатывающей промышленности, и их использование будет продолжать расти по мере того, как инженеры-технологи и технологи знакомятся с различными технологиями, необходимыми для обеспечения технологичности.Во второй статье этой серии из двух частей будут освещены некоторые из этих методов и проблем, которые следует учитывать при обработке эти сорта.
Ссылки
1. J.R. Fekete, A.M. Стибич, М.Ф. Ши, «Сравнение реакции HSLA и двухфазной листовой стали при динамическом раздавливании», Общество автомобильных инженеров (SAE), 2001-01-3101.
2. Камура М., Уцуми Ю., Омия Ю. и Кавамото Ю. «Ударопрочность и точечная сварка стального листа DP800, отожженного гальваническим способом», Общество инженеров автомобильной промышленности (SAE), 2001-01-3094.
.